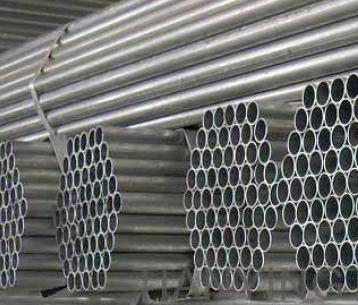
Since the discovery of oil in Saudi Arabia in 1938, the country’s economy has grown exponentially, along with its hydrocarbon infrastructure. Over the last two decades, Yanbu Steel has become the country’s largest indigenous fabricator of specialist structures.
Sitting on a fifth of the world’s petroleum reserves, Saudi Arabia is the world’s largest exporter, and has a huge downstream processing industry. It was in 1980 that on invitation of the Royal Commission for Jubail and Yanbu, an autonomous organisation of the Saudi government, the American company PDM set up operations in the Red Sea port of Yanbu to manufacture storage tanks and pressure vessels. “That company came in to support the projects of the Royal Commission here in Yanbu,” says Saad Omer, today general manager of Yanbu Steel. “It was a well established and experienced company that created a lot of jobs and stimulated local industry in the town.”
In 1995, PDM Inc. USA—the parent company of PDM Saudi Arabia—sold out to another US company, Chicago Bridge and Iron (CBI). The licensing agreement of PDM’s local Saudi partners with its US counterpart had five years to run, and at the end of that time the company was reconstituted as Yanbu Steel. In 2000, its shares were acquired by the Midroc Group, owned by the Saudi businessman Sheikh Mohammed Hussein Al Amoudi.
Today, CBI remains Yanbu Steel’s principal competitor in Saudi Arabia.“There is always competition but we are regarded as one of the best. Our clients, from nationally constituted oil and infrastructure companies like Aramco and the Saudi Basic Industries Corporation(SABIC) to operators like Marafiq, SEC or SWCC, who demand the highest standards, have given us many accolades.”
The company’s diverse facilities are located at Yanbu Steel’s facility in the industrial area of the west coast port. There is also a branch office at Dammam on the east-facing Gulf coast, Omer explains. “The main facilities are on a single site where we have a big facility occupying about 135,000 square metres, including a covered area of 35,000 square metres.” This is further subdivided into four principal areas: a tank and pressure vessels workshop linked to the plate and profile workshops, between them covering 20,000 square feet; and separate light workshops for structural fabrication along with a painting and blasting shop, accounting for a further 10,000 square metres; and office space.
The company’s core business is focused on the high specification steel vessels and specialised process equipment that are a feature of oil installations all over the world but which have come to define the industrial parts of Saudi Arabia’s landscape. “Our fundamental purpose is the manufacture and installation of API 650 and 620 storage tanks, pressure vessels, process columns, reactors, heat exchangers, evaporators and the like.” API, the American Petroleum Institute, and ASME, the American Society of Mechanical Engineers, he adds, set the internationally accepted standards for these items in terms of performance and quality.
Development capital is rarely a problem for Saudi companies, but joining the Midroc acquisition brought Yanbu Steel many valuable synergies. There are 16 separate entities within Saudi Arabia alone (Midroc is headquartered in Sweden, with operations in Ethiopia and Lebanon as well) and sister companies specialising in transportation, civil engineering, construction, pipelines and other contingent industries.
The value of these synergies has been demonstrated in many projects, but is perhaps best illustrated by the engagement of Yanbu Steel together with Midroc’s ABV Rock, a high-end construction company, as the EPC contractor, and the pipeline specialist Metal Services together with many other Saudi businesses, in the underground hydrocarbon storage megaproject. Spread over a number of locations, this started at the close of the 1980s with the goal of establishing the kingdom’s secure strategic oil reserves, and was completed in 2008. At its height it employed 12,000 people.
With over 1,200 employees Yanbu Steel is also an upcoming EPC contractor in its own right for tank farms and oil depots. These contain storage tanks of widely differing capacity, but they all have one thing in common—the need for 100 per cent quality and security. A leak on one of these sites where millions of gallons are stored would be a potential fire and environmental disaster.
Yanbu Steel does two types of fabrication: in the shop and in the field, explains Omer. “We also do quite a bit of brownfield work, including on-site tank construction and the repair and maintenance of the larger tanks and pressure vessels.” The company has recently invested $5.3 million in the modernisation and automation of its field welding systems.
Of course, state-of-the-art equipment calls for a high degree of competence in the operators, so Yanbu Steel puts a strong emphasis on training. It is a proactive contributor to the kingdom’s Saudization programmes, which aim to train and employ as many Saudi nationals as possible within the oil industry. “We have expatriates working in the company from all over the world, and they transfer their skills on the job. However there is a lot of local training available. We take on well qualified people from our universities and of course we look for qualified tradesmen like welders and fitters when we can get them. Others we take on untrained, and give them on the job training and instruction.”
Yanbu Steel now employs a fair proportion of Saudi welders, many of them trained in the company’s own technical academy. “We don’t just train welders—we test them all regularly and rigorously there. It is a resource for local industry as much as for Yanbu Steel because it provides a pool of qualified people in the industry. Many welders who have been trained up by us end up working for other companies, who recognise the quality of this training.”
As well as technical training, the school drums in the principles of quality control, safety and environmental awareness that Omer is determined will be appreciated by every client. “Quality is our watchword and we take great pains to make sure that our quality is the best and that safety takes a very high place in everything we do. Our LTA and reportable accidents are almost at zero and our QC problems just do not seem to exist. This gives us the edge over so many others and we find that because of these two very active programmes our efficiency and productivity actually improves.”
Quality counts. If people simply go with the lowest quote when they look for a partner to build a single vessel or a tank farm, they can end up with lost time, extra cost, rework and loss of profit, he says. Yanbu Steel doesn’t do that.